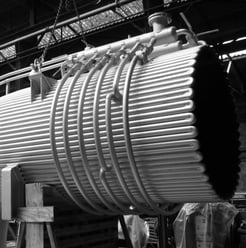

PROjects & DESIGNS
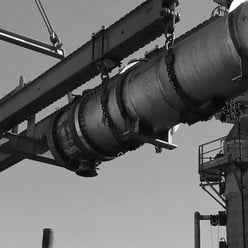
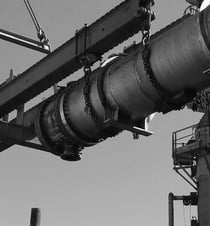
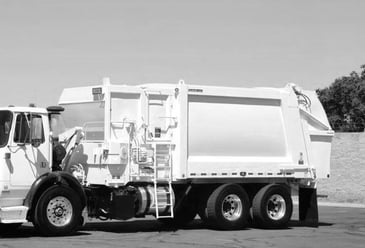
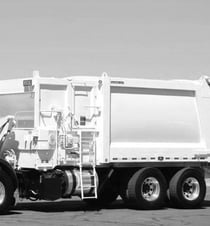
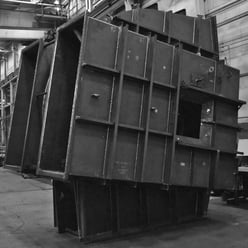
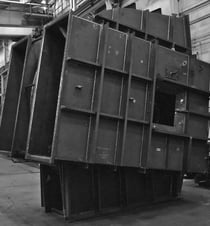
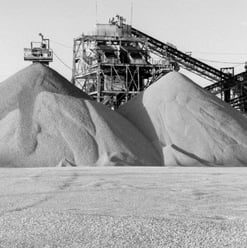
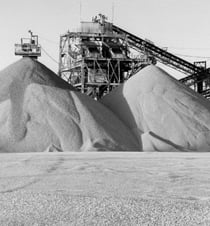
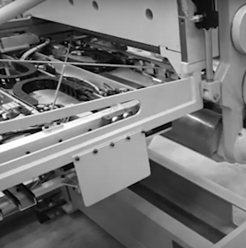
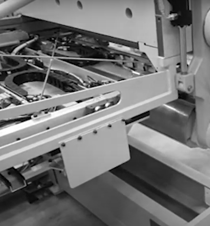
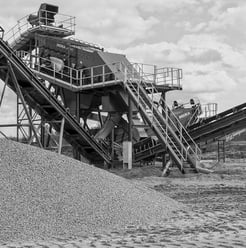

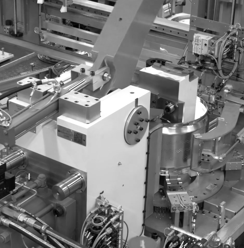
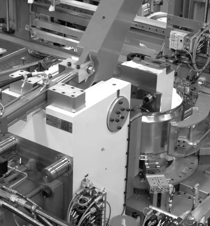
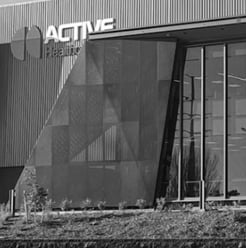
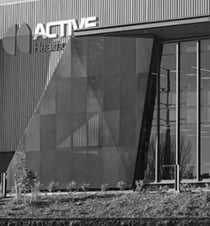
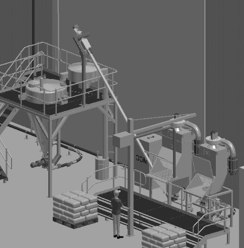
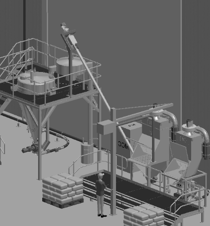
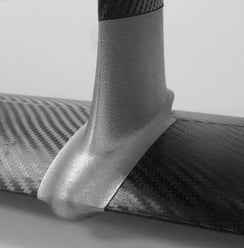
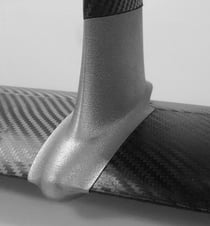
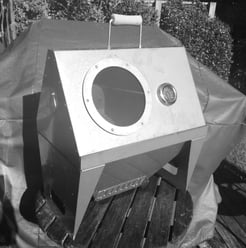
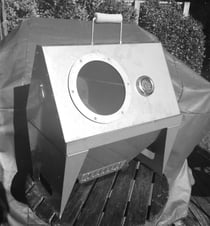
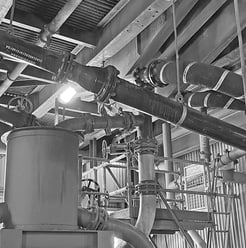
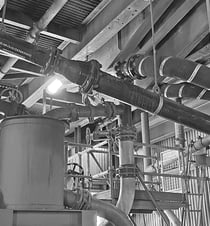
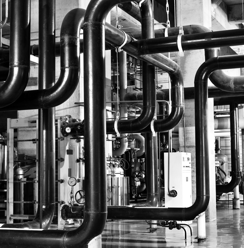
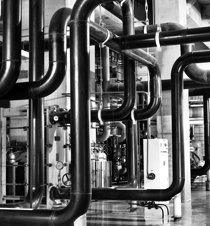
JUST FOR FUN
CHARCOAL BBQ PROTOTYPE - THE "TRI-BRAAI"
Charcoal fueled stainless BBQ that suits a standard 480x320mm grill
Developed in concert with Chilean Wife (They take BBQ seriously!)
Viewport to view delicious morsels
Thermometer to ensure caramelisation temperature met
Adjustable air-vent below to modulate charcoal burn
Still in use after over 4 years and scores of successful BBQs 😎
DESIGN ENGINEERING PROJECTS
*Note that certain images are replaced with a similar representative image to protect client confidentiality
**Projects are from most to least recent
REFRIGERATION PIPE BRIDGE & PIPELINES
Pipe bridge and lines for refrigeration service of a dairy factory
Developed in concert with certifying, structural, and process engineers
Full-length 2-tonne gantry beneath the bridge to service pumps and motors
Structure treated as IL3 (Seismic Requirement Importance Level 3 - High Value Contents)
Majority of stainless 304 pipes lagged
Fab and assembly steps planned so that fully painted bridge with pipes within could be transported and landed as one
Designed to tie-in with adjacent pipe bridge and future heat-recovery lines
Worked with electricial team to ensure cable-tray supporting and site install would be seamless
FURNACE FUME HOOD ELBOW
A water-cooled fabricated elbow for a furnace fume extraction system
Designed off an old set of drawings from the 1980's. Modern design and processing methods implemented to speed up fabrication and increase precision
Precise CNC tube-lasered jig fabricated to minimise weld-distortion and precisely locate headers and tubes
2x sectional-rolled headers
120x unique CNC tube-bent boiler tubes
Laser-scanned throughout fabrication to check tolerances met
Existing (old) elbow scanned for distortion to ensure assembly would be successful
Shotcrete refractory lined stab-in sensor locations
Over 2km of welding!
5 tonne, 1 off fabrication
ABRASION-PROOF VACUUM IMPELLER HOUSING
One of two monstrous housings for Ø2 metre vacuum impellers at an industrial plant
Redesign of impeller housing to withstand extraordinarily abrasive media that is torn through it
Internal faces clad with Duroxite (chromium-rich overlay plate) or Hardox 500 (abrasion-resistant steel)
Custom bolt and nut-shields to be black-nitrided tool steel
Impeller housing to be fabricated to critical tolerances (clearances to impeller)
4m x 4m x 4m (length x width x height), 6 tonne
CHEMICAL PLANT - HEAT EXCHANGER MONORAIL & PLATFORM
Platform and monorail to service heat exchanger (HX) at a Chemical Plant
Location of platform selected to minimise re-routing of existing pipelines
All work bolt-in-place with site mag-drilling. Minimal hot-work required.
Seismic clearance to HX silo allowed for
Packers and slotted holes facilitated mounting into the old existing steel structure
MUNICIPAL RUBBISH TRUCK - SWISS 22m³
Organisation of the manufacture of the first in a line of swiss rubbish-trucks
Worked in concert with vehicle consultant, fitters and OEM engineer
Organising the processing of OEM manufacture files by various suppliers
Custom design of mounts of bin subframe to a variety of trucks
3D scans used to facilitate mounting of bin, subframe and hydraulic lifter to truck
Production now humming for NZ-based fabricator!!!
MOBILE MINING PLANT - FINAL STAGE PURIFYING
Mobile plant used for fine-screening of material using magnetic separators and centrifuges
Developed in concert with certifying and mining engineer
25m x 15m x 15m (length x width x height) 250 tonne (Yes it is still mobile!!!)
Tanks (capacitors between screening stages) and poly-panel clad MCC room on first level
Centrifuges coupled with magnetic separators mounted on second level
Small-footprint water-recovery cyclone battery
Extensive slurry and water spooling with some custom-rolled piping (as flow-rate critical)
Extensive platforms to access all levels of plant
Observation hut mounted on plant
Plant able to be towed or pushed by mine bulldozers
MOBILE MINING PLANT - FIRST SCREENING
Mobile plant used for rough-screening of material using a shaker screen
Developed in concert with certifying engineer and mining engineer
10m x 12m x 10m (length x width x height) 150 tonne (Yes it is still mobile!!!)
Horizontal shaker screen mounted near max height to ensure correct angle of repose was met in the main tank below
Overflow tank mounted adjacent to capture water for spray-bars (for the screen)
Spray bars use a novel yet robust method to clear debris from nozzles (first of it's kind in use)
Poly-panel clad MCC (motor control centre) designed and mounted on skid behind main tank
Extensive platforms to access all levels of plant
Plant able to be towed or pushed by mine bulldozers
PROCESS MACHINERY - HOT WATER CYLINDER LINE - ROLL UP & HEM MACHINE
Process machine to convey a stainless sheet (hot water cylinder blank) to a rotating mandrel that will roll the sheet into a cylinder and press the seam to mechanically hold in place.
Developed in concert with design engineers, control systems engineers, fitters and machinists
Sheet translated using a vacuum cup grid assembly on linear rails
Welded structure machined to meet tight tolerances
Structure designed to be keyed together to aid in accurate assembly
PROCESS MACHINERY - WASHING MACHINE DRUM LINE - PATTERN EMBOSSING MACHINE
Process machine to take a washing machine drum blank, clamp securely and then press an embossed pattern into the drum using a punch and die
Developed in concert with design engineers, control systems engineers, fitters and machinists
Drum would then rotate 60°, five times and repeat the emboss after each rotation
Position fine-adjusted using camera feedback to servo-motor
Hydraulic cylinders used to press pattern and lock retaining arm in place
The required pressed form was complex requiring careful surface modelling
Press tools CNC machined using D2 tool steel
FOODSTUFF HANDLING EQUIPMENT FOR CAKE FACTORY (YUM!)
Equipment to move flour and sugar through a factory
Developed in concert with design engineers and process engineers
Design of stainless bag dumps, hoppers, screw conveyors and negative pressure pipelines for sanitary environment
Placement of explosion isolation valves in spooling (flour and sugar may be explosive if aerated...)
Design of platforms to service equipment
TITANIUM ADDITIVE MANUFACTURE
3D printing in metal! (specific experience in Ti64 EBM)
Experienced in the manufacture of components from multiple industries (performance vehicle engines, America's Cup foiling yachts, satellites - yes the ones in space, biomedical implants (hips, knees, skull-plates and elbows) for animals and people, osseointegral meshes - metal meshes that bones merge into)
Experienced in all aspects of processing components (surface finishing, heat-treating, machining, cleaning, bonding with carbon-fibre, quality control)
SPOOLING - MISCELLANEOUS
Various projects
Carbon steel lines using ERW, seamless and boiler tube
Stainless sanitary lines using dairy tube (ID tube), spiral welded (OD tube) and schedule pipe
Finishes specified as lagged (insulated), rubber-lined (for abrasive slurries), painted or bare stainless
Media of water, steam, gas, glycol, slurry, flour and sugar
Flanges of weldneck, RFSO/ FFSO, Neck ring and backup or triclover
Supported on shoes, suspended from above, nested in a pipe-bridge or snaking through a cake-factory
ARCHITECTURAL - MISCELLANEOUS
Various projects
Converting architectural concepts and drawings to elegantly processed/ fabricated parts
Experience in stainless, aluminium, corten (weathering steel), perspex and painted carbon-steel
Ballustrades, façades, stairways and more
Aesthetics at the forefront of thought, ease of assembly/ fabrication close behind
DRAFTING PROJECTS
MINE CONVEYOR REPLACEMENT & MATERIAL DISTRIBUTORS
An ancient conveyor was to be replaced by a new slurry pipeline to move material up to rotary screens (trommels)
Developed in concert with mine consultants
Monorails, hoppers, support structure and rubber-lined slurry line and make-up water lines drawn-up
Enormous custom fittings (Wyes) designed to split slurry line
2x sets of radial distributors and towers designed to distribute material to magnetic separators
Time and money saved by selecting more-appropriate paint-spec and facilitating fabrication by arranging for CNC processed material and templates